Honda HR-V: Reassembly - CVT Transmission Disassembly and Reassembly (CVT)
NOTE:
- Refer to the Exploded View as needed during this procedure.
- Keep all foreign particles out of the transmission.
- When you reassemble the transmission, apply a light coat of clean
transmission fluid on all oil seals, O-rings, and bearings. Also soak the
forward clutch assembly and the reverse brake discs,
in clean transmission fluid for at least 30 minutes prior to installation.
1. Reverse Brake Piston - Install
.png)
- Install the reverse brake piston (A) with new O-rings (B)
- Install the spring retainer/return spring (C).
.png)
- Put the reverse brake spring compressor attachment on the spring
retainer/return
spring assembly (A).
NOTE: Be sure the attachment is set over the return springs, not on the
reverse brake
piston (B)
- Install the reverse brake spring compressor plate (C) with facing the UP
mark to the
upside using bolts (D)
- Make sure that the reverse brake spring compressor bolt (E) is properly
installed on
the dent in the surface of the reverse brake spring compressor attachment
(F)
- Compress the return springs using the reverse brake spring compressor
until the
snap ring securing the spring retainer/return spring can be installed
- Install a new snap ring (G).
NOTE:
- Be careful not to deform the snap ring by opening/closing it
excessively.
- Make sure the snap ring is firmly installed in the groove.
- Remove the reverse brake spring compressor.
2. Reverse Brake Disc and Plate - Install
.png)
- Install the disc spring (A).
NOTE: Be sure to install the disc spring with the indented mark (B) facing
the
upward.
- Starting with the reverse brake plate (C), alternately install the
reverse brake plates
and the reverse brake discs (D).
- Install the reverse brake end-plate (E) with the flat side toward the
top disc.
- Install a new snap ring (F).
NOTE:
- Be careful not to deform the snap ring by opening/closing it
excessively.
- Make sure the snap ring is firmly installed in the groove.
3. Reverse Brake End-Plate Thrust Clearance - Inspect
- Set a dial indicator (A) on the reverse brake end-plate (B).
.png)
- Zero the dial indicator with the reverse brake end-plate is lifted up to
the snap ring (C)
- Release the reverse brake end-plate
- Put the clutch compressor attachment and the clutch compressor
attachment 64 mm on the reverse brake end-plate
- Press the clutch compressor attachment down with 39 N (4.0 kgf, 8.8 lbf)
(the weight of the clutch compressor attachment is included) using a force
gauge, and read the dial indicator
- The dial indicator reads the clearance (D) between the reverse brake
end-plate and the top disc (E). Take measurements in at least three places,
and use the average as the actual clearance.
Standard: 1.0-1.2 mm (0.039-0.047 in)
- If the clearance is out of the standard, remove the reverse brake
end-plate and select a suitable one.
- 3.6 mm (0.142 in)
- 3.7 mm (0.146 in)
- 3.8 mm (0.150 in)
- 3.9 mm (0.154 in)
- 4.0 mm (0.157 in)
- 4.1 mm (0.161 in)
- 4.2 mm (0.165 in)
- 4.3 mm (0.169 in)
- 4.4 mm (0.173 in)
- 4.5 mm (0.177 in)
- 4.6 mm (0.181 in)
- 4.7 mm (0.185 in)
- 4.8 mm (0.189 in)
- 4.9 mm (0.193 in)
- 5.0 mm (0.197 in)
- Install a selected reverse brake end-plate, then recheck the clearance.
4. Sun Gear, Planetary Carrier, and Ring Gear - Install
.png)
- Install the ring gear (A), the thrust washer (B), and the collar (C) as
shown
- Install the planetary carrier (D) and the thrust needle bearing (E) as
shown
- Install the 33 x 40 mm thrust shim (F) and the sun gear (G)
- Install a new snap ring (H) using the snap ring pliers.
NOTE:
- Be careful not to deform the snap ring by opening/closing it
excessively.
- Make sure the snap ring is firmly installed in the groove.
5. Sun Gear Thrust Clearance - Inspect
- Set a dial indicator (A) on the sun gear (B).
.png)
- Zero the dial indicator with the sun gear is lifted up to the 33 x 40 mm
thrust shim (C) contact the snap ring (D)
- Release the sun gear
- Put the clutch compressor attachment on the sun gear
- Press the clutch compressor attachment down with 49 N (5.0 kgf, 11.0 lbf)
(the weight of the clutch compressor attachment is included) using a force
gauge, and read the dial indicator
- The dial indicator reads the clearance (E) between the sun gear and the
33 x 40 mm thrust shim. Take measurements in at least three places, and use
the average as the actual clearance.
Standard: 0.04-0.09 mm (0.0016-0.0035 in)
- If the clearance is out of the standard, remove the 33 x 40 mm thrust
shim and select a suitable one.
- 1.31 mm (0.0516 in)
- 1.34 mm (0.0528 in)
- 1.37 mm (0.0539 in)
- 1.40 mm (0.0551 in)
- 1.43 mm (0.0563 in)
- 1.46 mm (0.0575 in)
- 1.49 mm (0.0587 in)
- 1.52 mm (0.0598 in)
- 1.55 mm (0.0610 in)
- 1.58 mm (0.0622 in)
- 1.61 mm (0.0634 in)
- 1.64 mm (0.0646 in)
- 1.67 mm (0.0658 in)
- 1.70 mm (0.0669 in)
- 1.73 mm (0.0681 in)
- 1.76 mm (0.0693 in)
- 1.79 mm (0.0705 in)
- 1.82 mm (0.0717 in)
- 1.85 mm (0.0728 in)
- Install a selected 33 x 40 mm thrust shim, then recheck the clearance.
6. Stator Shaft and Input Shaft - Install
- Install new sealing rings (A).
.png)
- Check the needle bearing (B). If the needle bearing is worn or damaged,
replace it
- Install the input shaft (C) by aligning the clutch discs (D) with the
splines (E)
- Install a new sealing ring (F)
- Install the stator shaft (G) with the 26 x 38.8 mm thrust shim (H) and
the thrust needle bearing (I) as shown.
7. Transmission Fluid Lubrication Pipe and Baffle Plate - Install
.png)
Fig. 40: Baffle Plate With Torque Specifications
- Install the transmission fluid lubrication pipe (A) by aligning the
guide tab (B) with
the guide hole (C)
- Install the baffle plate (D).
8. Oil Pump Drive Sprocket Sealing Ring - Install
.png)
- Install a new sealing ring (A).
9. Manual Valve Body and Stator Shaft Flange - Install
.png)
Fig. 41: Manual Valve Body and Stator Shaft Flange With Torque Specifications
- Install the stator shaft flange (A) with the dowel pins (B) (C) by
aligning the
transmission fluid lubrication pipe (D) and the dowel pins (B) with the
mounting holes
(E)
- Install the manual valve body (F) with the separator plate (G) and the
dowel pins
(H).
10. Control Shaft - Install
.png)
Fig. 42: Control Shaft With Torque Specifications
- Install the detent lever (A) by aligning the guide tab (B) with the
groove (C).
- Install the control shaft (D)
- Install the roller (E) by aligning the mounting hole (F) with the groove
(G)
- Secure the control shaft with a new lock washer (H), then pry up the
lock tab (I) of the lock washer against the bolt head
- Install the detent spring (J).
11. Transmission Fluid Pump Drive Sprocket and Transmission Fluid Pump Drive
Chain - Install
.png)
- Install the transmission fluid pump drive sprocket (A) and the
transmission fluid
pump drive chain (B)
- While expanding a new snap ring (C) of the transmission fluid pump drive
sprocket
using the snap ring pliers, install the transmission fluid pump drive
sprocket.
NOTE:
- Be careful not to deform the snap ring by opening/closing it
excessively.
- Make sure the snap ring is firmly installed in the groove.
12. Final Drive Shaft and Differential Assembly - Install
.png)
- Install the final drive shaft assembly (A) and the differential assembly
(B).
13. Torque Converter Housing - Install
.png)
- Remove all of the old liquid gasket from the mating surfaces of the
transmission
housing and the torque converter housing, the bolts, and the bolt holes
- Clean and dry the mating surfaces of the transmission housing and the
torque
converter housing
- Apply liquid gasket (Honda Genuine Liquid Gasket 5460H) to the
transmission
housing surface and to the inside edge of the threaded bolt holes. Install
the
component within 4 minutes of applying the liquid gasket.
NOTE:
- Apply a 1.5 mm (0.059 in) diameter bead of liquid gasket along the
broken line
(A) which is 3.9 mm (0.154 in) from the chamfering surface of the
transmission
housing inner side.
- Do not apply any liquid gasket to the bolt hole.
- Apply the liquid gasket all around as shown. When the bead is
arriving at the
end point, overlap the liquid gasket.
- The torque converter housing must be installed within 4 minutes. If
too much
time has passed after applying the liquid gasket, remove the old liquid
gasket
and residue, then reapply new liquid gasket.
- Do not touch the applied liquid gasket face.
.png)
Fig. 43: Torque Converter Housing With Torque Specifications (2WD)
.png)
Fig. 44: Torque Converter Housing With Torque Specifications (AWD)
- Install the torque converter housing (A) with the dowel pins (B), and
tighten the
bolts in a crisscross pattern in at least two steps.
NOTE:
- Wait for at least 1 hour before filling the transmission with
transmission fluid.
- Do not run the engine for at least 3 hours after installing the
torque converter
housing.
14. Parking Brake Pawl - Install
.png)
Fig. 45: Parking Brake Pawl With Torque Specifications
- Install the parking brake rod holder (A) and a new lock washer (B)
- Pry up the lock tab (C) of the lock washer against the bolt head
- Install the parking brake pawl (D) with the parking shaft (E) and the
parking pawl
spring (F).
15. Transmission Fluid Pipe and Transmission Fluid Cooler Pipe - Install
.png)
Fig. 46: Transmission Fluid Pipe and Transmission Fluid Cooler Pipe With
Torque Specifications
- Install the transmission fluid pipes (A) with new O-rings (B)
- Install the transmission fluid cooler pipe (C).
16. End Cover - Install
.png)
- Install new sealing rings (A).
.png)
- Remove all of the old liquid gasket from the mating surfaces of the
transmission
housing and the end cover, the bolts, and the bolt holes
- Clean and dry the mating surfaces of the transmission housing and the
end cover
- Apply liquid gasket (Honda Genuine Liquid Gasket 5460H) to the
transmission
housing surface and to the inside edge of the threaded bolt holes. Install
the
component within 4 minutes of applying the liquid gasket.
NOTE:
- Apply a 1.5 mm (0.059 in) diameter bead of liquid gasket along the
broken line
(A) which is 3.9 mm (0.154 in) from the chamfering surface of the end
cover
inner side.
- If too much time has passed after applying the liquid gasket, remove
the old
liquid gasket and residue, then reapply new liquid gasket.
- The end cover must be installed within 4 minutes. If too much time
has passed
after applying the liquid gasket, remove the old liquid gasket and
residue, then
reapply new liquid gasket.
- Do not touch the applied liquid gasket face.
.png)
Fig. 47: End Cover With Torque Specifications
- Install the end cover (A) with the dowel pins (B), and tighten the bolts
in a
crisscross pattern in at least two steps.
NOTE:
- Wait for at least 1 hour before filling the transmission with
transmission fluid.
- Do not run the engine for at least 3 hours after installing the end
cover.
17. Transmission Fluid Pump - Install
.png)
Fig. 48: Transmission Fluid Pump With Torque Specifications
- Install the transmission fluid pump (A) with the dowel pins (B).
18. Solenoid Wire Harness - Install
.png)
Fig. 49: Solenoid Wire Harness With Torque Specifications
- Connect the connectors (A).
- Install the transmission fluid temperature sensor (B)
- Install the ground terminals (C) and the harness clamps (D).
19. Valve Body Assembly - Install
.png)
- Install the transmission fluid pipes (A) with new O-rings (B).
- Install the solenoid wire harness subconnector (A) with a new O-ring
(B).
.png)
Fig. 50: Valve Body Assembly With Torque Specifications
- Connect the connector (C)
- Install the valve body (D).
NOTE: Do not damage the solenoid wire harness (E) while installing the
valve body assembly.
Length of Bolt
F - 90 mm (3.54 in)
G - 65 mm (2.56 in)
20. Transmission Fluid Pan and Transmission Fluid Strainer - Install
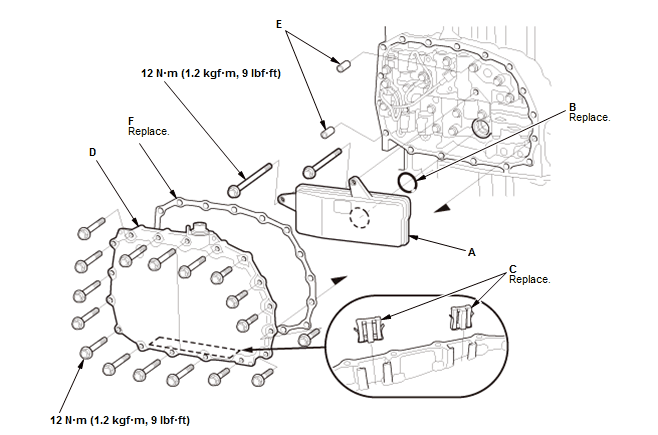
Fig. 51: Transmission Fluid Pan and Transmission Fluid Strainer With Torque
Specifications
- Install the transmission fluid strainer (A) with a new O-ring (B).
NOTE: Do not damage the solenoid wire harness while installing the
transmission fluid strainer.
- Install new magnets (C)
- Install the transmission fluid pan (D) with the dowel pins (E) and a new
gasket (F), and tighten the bolts in a crisscross pattern in at least two
steps.
NOTE: Do not damage the solenoid wire harness while installing the
transmission fluid pan.
21. Sensor - Install
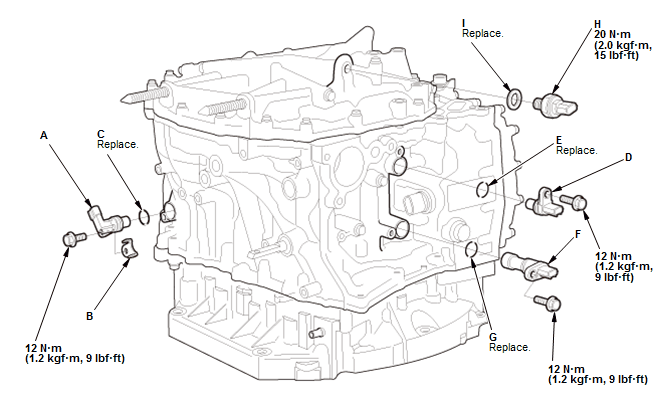
Fig. 52: Sensor With Torque Specifications
- Install the CVT speed sensor (A) with the sensor washer (B) and a new
O-ring (C).
- Install the CVT drive pulley speed sensor (D) with a new O-ring (E)
- Install the torque converter turbine speed sensor (F) with a new O-ring
(G)
- Install the CVT driven pulley pressure sensor (H) with a new sealing
washer (I).
NOTE: Be careful not to damage the plastic part.
22. Transmission Range Switch - Install
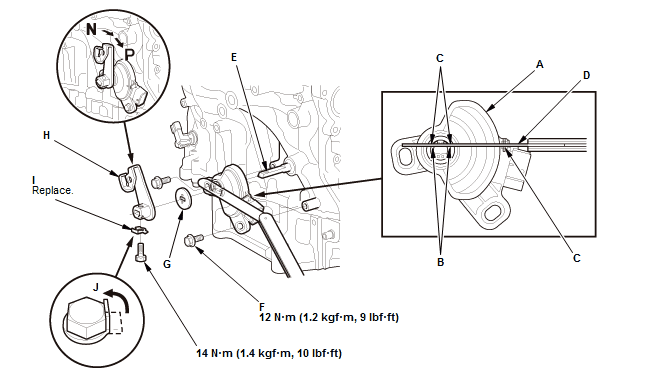
Fig. 53: Transmission Range Switch With Torque Specifications
- Set the transmission range switch (A) to the N position. Align the
cutouts (B) on the rotary-frame with the N positioning cutouts (C) on the
transmission range switch, then put a 2.0 mm
(0.079 in) feeler gauge (D) in the cutouts to hold the transmission range
switch in the N position.
NOTE: Be sure to use a 2.0 mm (0.079 in) feeler gauge or equivalent to hold
the transmission range switch in the N position.
- Install the transmission range switch gently on the control shaft (E)
while holding it in the N position with the 2.0 mm (0.079 in) feeler gauge
- Tighten the bolts (F) on the transmission range switch while you
continue holding the N position
- Remove the feeler gauge
- Install the control shaft cover (G)
- Install the control lever (H) with a new lock washer (I)
- Pry up the lock tab (J) of the lock washer against the bolt head
- Turn the control lever to the P position.
23. Transfer Assembly - Install (With AWD)
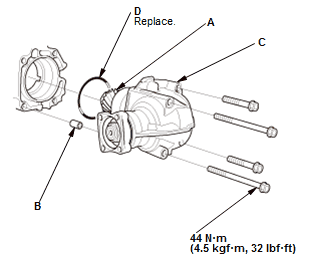
Fig. 54: Transfer Assembly With Torque Specifications
- Apply a light coat of clean transmission fluid to the transfer mount and
transfer
driven gear (A)
- Install the dowel pin (B)
- Install the transfer (C) with a new O-ring (D).
READ NEXT:
Special Tools Required
Driver Handle, 15 x 135L 07749-0010000
Attachment, 45 mm 07947-6890300
Bearing Separator 07KAF-PS30200
Exploded View
1. Final Drive Shaft - Exploded View
Disassembly
NOTE: T
Exploded View
1. Shift Lever Assembly - Exploded View
NOTE: Do not wipe off the special grease applied to the area of the shift
lever marked with an asterisk (*).
Fig. 55: Exploded View Of Shift Lev
Special Tools Required
Oil Seal Driver Attachment, 58 mm 07JAD-PH80101
Holder, Companion 07PAB-0020000
Driver, 32.5 mm 070AD-SAA0100
Driver Handle, 15 x 135L 07749-0010000
Exploded View
1. Transfe
SEE MORE:
CRUISE CONTROL SYSTEM DESCRIPTION - OVERVIEW
The cruise control system maintains a constant vehicle speed without the
driver pressing the accelerator pedal.
Operation
To operate the cruise control system, the driver must first turn on the
cruise/main switch. With the cruise/main
switch on, the cru
NOTE: Before you troubleshoot, review the how to troubleshoot the
electric parking brake system.
1. Problem verification:
Turn the vehicle to the ON mode.
Clear the DTC with the HDS.
Turn the vehicle to the OFF (LOCK) mode, then to the ON mode.
Check for DTCs with the HDS.
Is DTC C0031-62,